Forest fuel is trunks, branches, tops, bark and whole trees. Wood has traditionally been the most important fuel from the forest. In recent years, many heating plants have been built in the country using wood chips as an energy carrier. The supply chain from the forest to the heating plant has been mechanized. Continuous feeding of chips from the chip silo to the chip burner provides easy operation. The heat from a heating system is led on with the hot water that is heated from the tiled boiler. Water-borne heating systems can deliver heat to consumers both over short and longer distances, and provide great flexibility in the distribution of heat.
Climate benefit
Forests are a renewable resource. Photosynthesis in the leaves and needles of the tree captures carbon dioxide, CO2, from the atmosphere. This is converted into carbohydrates and further into cellulose and lignin in the wood. This makes up the tree's roots, trunk and branches. One cubic meter (m3) dry birch weighs 500 kg, and has bound one tonne of CO2. When trees die and rot, or if the wood is burned, CO is released2 into the atmosphere again. Carbon dioxide is recaptured from the atmosphere as the forest grows. That is why we say that forests are a renewable resource.
It has been common to set the climate effect to zero when we fire with biofuel. It can still be debated whether this is so. Some (fossil) fuel is used for cutting and transport and this is calculated at 9 g of CO2 per kWh for wood chips and 3 g CO2 per kWh for return chips. (Environment Directorate) . A tiled boiler will also be produced and this has a climate footprint, but we do not have very good figures for this. The combustion of wood chips emits CO2 and we can think that this enters the cycle and is bound when new trees grow up. But this takes some time, if the trees were allowed to grow and absorb even more CO2 we would have a positive climate effect in the short term, but in the long run this evens out.
Another way to calculate the climate benefit is to look at which heat source is replaced. If it is propane with emissions of 230 g CO2 per kWh, replacing it with bioenergy provides good climate benefits, regardless of how we calculate.
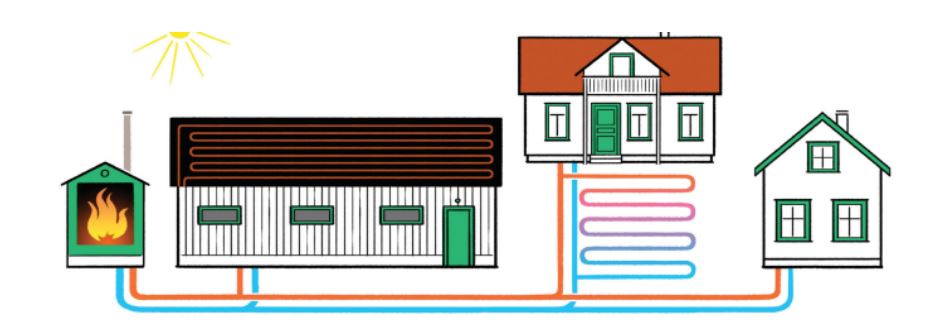
Drying and chopping wood chips
The moisture in fresh wood is about 50%, and must be dried down to 30% for it to work well in a heating system. When storing the wood in an airy and sunny place in the forest, it is possible to dry it against 30%. Many also make use of artificial drying of chips in a chip warehouse after the wood is chipped.
Powerful chippers are used for chopping wood chips. They can be freestanding or mounted on a tractor or truck. The largest have a large capacity, and e.g. the annual consumption of wood chips for a farm can be chipped in a short time. Most have covered tile warehouses for storing the tiles. The quality of the tile and the water content have a lot to say about the efficiency and operational reliability of the tile plant. It also helps to influence the lifespan of the tiled stove.
Calorific value
Calorific value is the energy released by complete combustion of the wood. The calorific value for dry wood chips is stated at 5.3 kWh/kg. This applies to both conifers and hardwoods. Damp wood chips have a lower calorific value. Larger tile plants can take tiles with higher humidity than smaller plants. In small plants, the humidity should be below 30-35 %. Damp wood chips can also cause problems with it freezing into lumps in the winter and causing operational problems in the plant.
Heat energy from a bio-heating plant
A modern bioheating plant has an efficiency of 85-90 %. Old wood stoves have an efficiency of 40-50 %, while newer stoves have an efficiency of up to 75 %.
Combustion in a tile plant takes place inside the tile boiler. The power of the tile boiler is given in kW (1000 Watt). Effect is defined as work performed per unit of time. Heat energy produced in a certain period of time (output x time) says something about the facility's physical size and capacity. Ex. a plant with an output of 50 kW, and which produces full output for 150 hours, provides an energy quantity of 7500 kWh (kilowatt hours). For a normal tiling system, it is usual to have an average usage time of around 2000 hours a year. With high electricity prices, the use of bioenergy becomes more profitable.
Task:
A farmer invests in such a (50kW) plant, and the plant must produce 100,000 kWh within a year. How many hours must the plant run to provide this amount of energy (assuming the plant runs at full capacity)? Than if the plant is run at 75 % performance?
The amount of wood chips is usually stated as the number of loose cubic meters (lm3). The tiles to be used in the facility provide approximately 700 kWh/lm3 tile. How many ch3 with wood chips helps to cover the annual heating needs on the farm?
In relation to solid mass, the chip volume is 3 times larger. How many m3 with forest is needed to cover the heat demand?